|
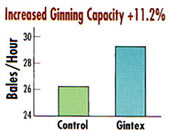
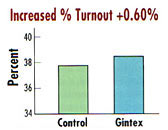
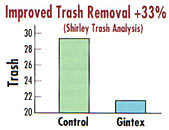
|
As seen in the graphs resulting from a uniform flow of cotton, Gintex Fiber Conditioner is able to increase ginning capacity by an average of 11.2% without adjusting the feeder rates; improve the % turnout by an average of 0.60 percent, while increasing trash removal for improved cotton grades.
This goes against normal ginning trends which show an 11.2% increase in ginning capacity would reduce % turnout and lower cotton grades! (USDA's "Ginning for Maximum Grades").
Extensive trial testing supported by over half of the U.S. ginning industry committed to this new technology verify.
- Greater turnout
- Greater capacity
- Superior cotton grades
- Improved fiber quality in every run
Considering the mechanics of this technology relying on reduced fiber to machinery friction, these claims are not surprising. For example, reduced friction eliminates the build-up of positive ions on a cotton fiber to the negative ions of foreign matter otherwise known as static electricity.
A static free processing environment improves the separation of foreign matter from fiber increasing % turnout, improving cotton grades, and encouraging a uniform flow of cotton to improve ginning capacity.
Cotton treated with Gintex'M Fiber (conditioner flows smoothly through the cleaning and ginning machinery, with lower energy costs and less chokes. This, in turn, increases processing efficiencies resulting in higher bottom-line profits.
"Make no mistake....through the use of the HVI system, mills recognize and are beginning to quantify efficiencies gained throught the use of superior cotton in their spinning plants." With Gintex, you are able to meet your processing requirements while providing the textile industry with quality fiber needed for today's high speed processing machinery. The Cotton Gin and Oil Press. |
|
By creating a friction-free processing through this mechanical process eliminating damage. Test results show while increasing environment, ginning cotton fibers flow uniformly wading and bunching associated with fiber capacity by 13.1% via a uniform flow of cotton, treated fibers maintained their original fiber characteristics while increasing the trash removal as noted by a higher Rd value (brightness).
When comparing the % of short fibers (loss than 112th), and non treated cotton again showed a remarkable improvement. This is especially apps*wW when processing immature fiber. For the first time GintexTM Fiber Conditioner provides the ginning industry with the option of reducing drying temperatures without a loss of production. In turn, lower dryer temperatures help preserve fiber quality.
If ginning capacity is your goal, decision would be to bring your ginning competitiveness. Just think of the time and end-user you'll machinery satisfaction is your mission, then a timely up to speed to meet world-market save with Gintex.
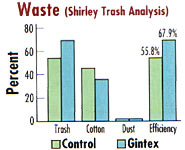
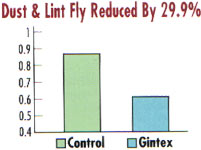
|
Time to quit spinning your wheels
Gintex's conditioning system brings your fiber up to speed by preserving the natural wax-like surface allowing fibers to be processed in a timely, cost efficient manner. Operating your equipment without GintexTM is like taking a step back in time
Improved Cleaning Without The Loss Of Fiber
With the cost of raw materials accounting for 40% to 60% of the yarn costs, it's becoming critically important to maximize your profits through an efficient cleaning process that will remove foreign matter without the loss of valuable fiber.
Gintex Fiber Treatment System reduces fiber to machinery friction eliminating static electricity which impedes the separation between trash and foreign matter. As a result, foreign matter moves to its proper location, while good spinnable fibers continue ending up in the yarn. The standard calculation of cleaning efficiency showed a 12.1% increase in trash removal while a closer examination of the waste collected from the pre-cleaning machinery measured a higher percentage of trash, and cotton dust, while accumulating fewer good spinnable fibers.
A gentler cleaning and processing environment reduces fiber damage (short and frazzled fibers), associated with lint fly and dust deposits. Using dust collection ventilators mounted on top of cards 1 through 8, treated cotton measured an average 28.6% reduction in dust and lint fly. Further studies show collected fibers and dust deposits surrounding the top and bottom roll cylinders measured a 24% reduction by weight. Good spinnable fibers collect in the filter box were reduced by 20 .40% depending on the process. |
Department of quality control certified no difference in dye intake between control and treated yarn samples. |
Increased Yarn Quality and Improved Production
In today's high speed machinery, frictional values exceed the limit set by the natural wax-like surface located within the cuticle of a fiber.
As a result, fiber damage begins to occur during the harsh ginning environment and continues throughout the pre-cleaning and spinning process.
Gintex Conditioning Agents preserve this wax-like surface by reducing fiber to machinery friction which causes an excessive amount of fiber breakage otherwise known as short fiber. As seen in Mill 1, test results show improved fiber preparation increased yarn quality reducing the number of ends down by 35%.
"With the application of Gintex, we noticed a significant difference is comparative results: twenty-five percent reduction in returnable fiber, as well as a twenty-five percent decrease In dust and lose fibers surrounding the areas significant to the spinning process. Uster analysis recorded a 6 percent increase in yarn strength, 13 percent decrease in elongation, and a 15 percent decrease Is CV percent,"
Control of Quality |
Results from Mill 2 show a uniform flow of cotton having reduced static electricity allowed the fiber to pass freely through the carding, combing, roving and spinning process reducing the number of roller laps, increasing production throughout the textile process.
Through improved cleaning and a gentler processing environment, Gintex™ decreases the number of neps throughout the cleaning, carding, combing and spinning process.
A Sticky Situation
With a growing number of cotton bales containing an excessive amount of sugar deposits which are being circulated through our marketing system, problems in spinning will continue to change the way fiber is being processed. |
|
Return on Investment
To view additional test results showing the return on your investment , click here.
Gintex's™ conditions both fiber and machinery reducing the buildup of sugar deposits on the rollers and processing machinery. Improved cleaning removes sugar specks prior to processing.
While processing cotton containing an excessive amount of sugar, Gintex allowed my spinning mill to maintain slightly below normal processing rates which otherwise would not have been possible."
Spinning Manager |
Gintex, the gentle conditioner
APPLICATION: Gintex is sold as a liquid concentrate in 208 liter (55 gal.) drums ready for use. Under normal processing conditions, we recommend 0.44 liters (0.93 pints) per 220 Kg bale (485 lbs.) bole. One drum will treat 472 boles, or 103,840 Kg of lint. The application rate is adjustable to meet the demands of processing conditions.
APPLICATION PROCEDURE: Gintex is applied using an easy-to-install spray atomizing dispensing unit. Controlled by a manual on/off switch, or electric eye, the dispensing unit creates a fog through which the cotton passes. The conditioning agents are dispersed throughout the cotton fiber and the processing machinery. the application point is adjustable to meet the demands of your processing machinery. For further questions, please consult your instruction manual or your local representative.
EQUIPMENT: The dispensing unit is sold complete, and ready to install with a solenoid, loot valve, air regulator, pump (sizes vary according to processing needs), warning light, air liquid lines and spray nozzle.
MECHANICALS: Gintex is a non oil-based/silicon based cotton fiber conditioner which reduces fiber to machinery friction. As a result, fiber and foreign matter move freely without static electricity in the direction intended. A uniform flow of cotton improves processing efficiencies and reduces fiber damage caused by a harsh processing environment.
OPTIONS: A 220/50 Hz transformer and electric eye.
|
|